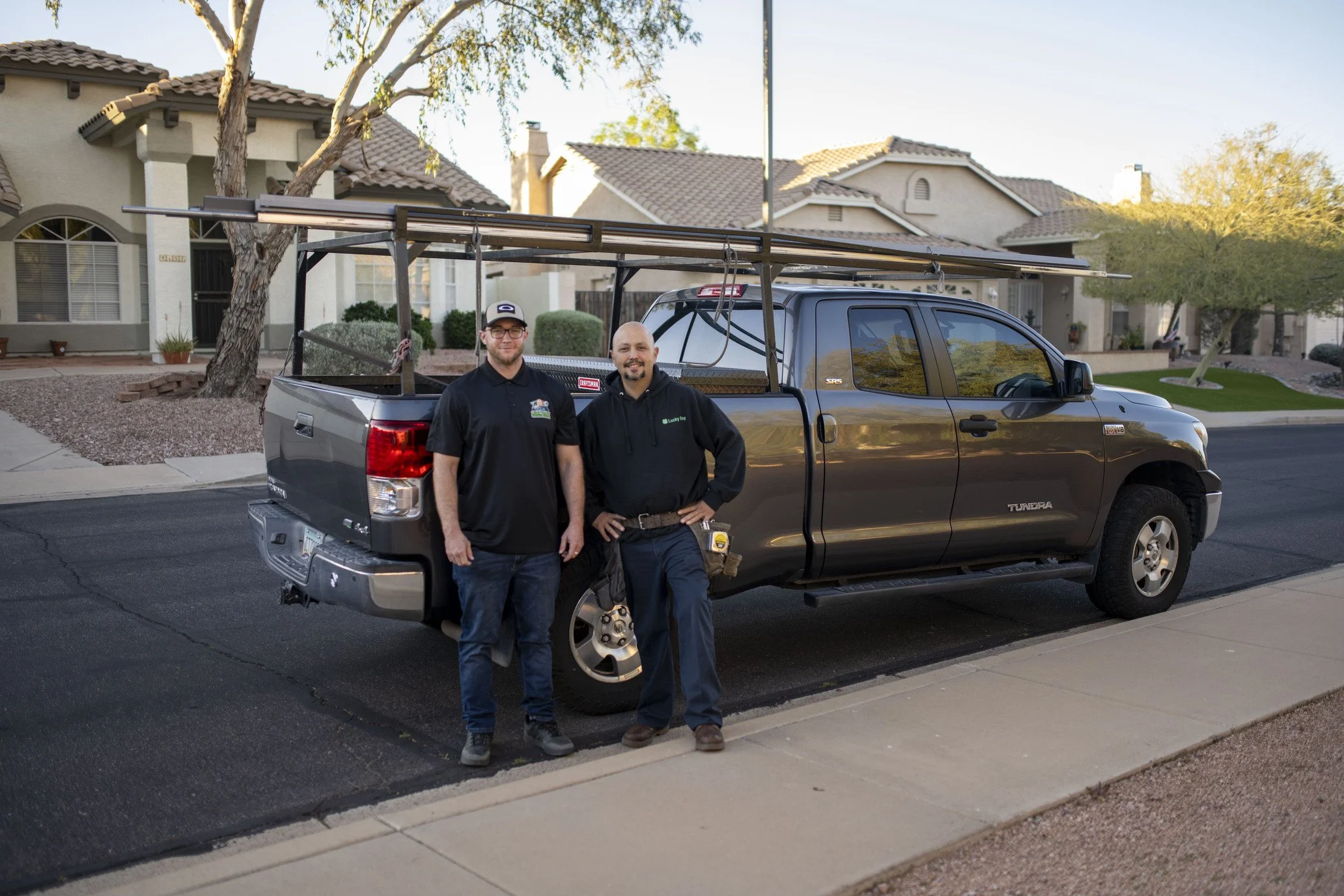
Garage Door Keypad Repair
Garage door keypads offer secure and convenient access without needing a remote or key. When the keypad stops responding, delays in opening or closing the garage become a daily frustration. Most keypads are designed to handle frequent use, but heat, moisture, and dust exposure can affect performance over time. Common problems include stuck buttons, non-responsive key entries, battery issues, or signal disruptions between the keypad and the opener system. Repairs begin with a complete inspection to identify whether the problem lies with the keypad or communication link.
After opening the housing, technicians look for signs of wear on internal contacts, water intrusion, or loose connections that might prevent the system from activating. If the keypad is still in working condition, it may only need a battery replacement, reprogramming, or cleaning to restore reliable function. Replacing the keypad often offers a quicker, more dependable solution when the circuitry is damaged, or components have reached the end of their lifespan. Compatibility is confirmed before installation, allowing for a smooth reconnect to the existing garage door opener.
Service includes testing for accuracy, range, and responsiveness to ensure the keypad performs as expected. New codes are programmed, hardware is mounted securely, and safety features are reviewed. Garage keypad repair services across Mesa, Phoenix, and surrounding areas provide fast access solutions while minimizing system downtime. Each repair visit is completed with focus and care, restoring entry access without affecting the rest of the garage door setup. Keypads are evaluated honestly, repaired when possible, and replaced when necessary.
Signs Garage Door Keypad Repair is Needed
-
An entirely unresponsive keypad represents one of the most common access issues garage door owners face. The system requires professional attention when pressing buttons, which produces no feedback - no beeps, no lights, no door movement. This complete lack of response typically indicates power supply problems or internal circuit board failures within the keypad unit. Batteries in wireless models naturally deplete over time, sometimes causing sudden failure rather than gradual performance decline. Wired keypads might experience connection issues where power from the central opener unit fails to reach the external control panel. Our technicians begin diagnosis by isolating power supply concerns before examining more complex electronic components that might require specialized repair techniques.
-
Few garage access issues create more frustration than keypads that work unpredictably from one attempt to the next. The sporadic nature of intermittent operation often coincides with specific environmental conditions like temperature changes or precipitation events. Moisture infiltration into the keypad housing sometimes creates temporary short circuits that resolve as components dry naturally. Internal connection issues where circuit board solder points develop microscopic cracks cause temperamental functionality that worsens over time. Battery-powered units frequently exhibit intermittent behavior as power cells approach the end of their useful life but retain partial charge. Our repair specialists utilize systematic testing procedures that recreate various operating conditions to identify precise causes of inconsistent performance before recommending appropriate solutions that restore reliable functionality.
-
The digital display serves as a feedback mechanism and visual confirmation of proper keypad operation. When display illumination diminishes or disappears, users lose critical input confirmation during code entry sequences. Backlighting elements gradually deteriorate over time, particularly in models exposed to direct sunlight, accelerating LED degradation. Power supply limitations sometimes affect display functionality before impacting other electronic components, creating a recognizable pattern of failure. Internal connection issues between the display module and main circuit board occasionally develop from thermal expansion and contraction cycles over years of temperature variations. Our diagnostic approach includes display component isolation testing that distinguishes between simple illumination issues and more complex electronic failures affecting the entire keypad system.
-
This particularly confusing symptom occurs when the keypad appears functional - accepting code inputs and displaying appropriate feedback - yet fails to activate the door mechanism. Communication breakdowns between the keypad and central opener unit typically cause this disconnection between input and operation. Radiofrequency interference sometimes blocks wireless transmission signals despite normal keypad behavior. Programming misalignment occasionally develops where the opener no longer recognizes previously valid access codes entered correctly. Receiver issues within the central opener unit might prevent proper signal interpretation despite standard transmission from the keypad. Our repair protocol includes comprehensive communication testing between system components to identify exact failure points in the command chain from keypad input to physical door operation.
-
When a noticeable lag develops between code entry and door activation, underlying communication inefficiencies typically require attention. These delays often progressively worsen over time as components deteriorate further. Signal strength degradation in wireless systems creates extended processing times as the opener repeatedly attempts to interpret weakened transmission data. Processing capabilities within aging circuit boards sometimes diminish, extending response times despite normal functionality. Radiofrequency congestion in densely populated neighborhoods occasionally delays transmission as multiple devices compete for bandwidth. Battery-powered units operating with diminished power reserves might maintain functionality while experiencing slower processing capabilities. Our technicians measure response timing during diagnostic procedures, comparing results against manufacturer specifications to determine when delays exceed acceptable parameters.
-
This puzzling situation creates confusion when the keypad appears to function normally but fails to initiate door movement. The illuminated response suggests that the power supply remains adequate while indicating a different malfunction category elsewhere in the system. Internal microprocessor errors sometimes allow normal power distribution without proper command processing capabilities. Transmission components occasionally fail independently from input recognition systems, creating a disconnection between seemingly regular operation and actual door control. Programming corruption within memory storage occasionally develops from power surges or battery failures, requiring a complete system reset. Our comprehensive testing methodology distinguishes between various potential causes by systematically eliminating each possibility and identifying the specific malfunction responsible for this misleading symptom pattern.
Common Causes of Garage Door Keypad Problems
-
Dead or Weak Batteries
Battery power depletion accounts for approximately sixty percent of all wireless keypad malfunctions reported to our service department. These power cells naturally deteriorate over time, typically lasting between nine and eighteen months, depending on usage frequency and environmental conditions. Cold weather significantly reduces battery efficiency, creating seasonal performance issues during winter when chemical reactions within batteries slow considerably. Extreme heat similarly affects battery performance by accelerating internal chemical degradation, reducing lifespan. Partial depletion creates confusing symptoms where the keypad functions sporadically or works only during warmer parts of the day when chemical reactions occur more efficiently. Our technicians recommend preventative battery replacement every nine months for wireless keypads exposed to extreme temperature variations to maintain consistent performance throughout seasonal changes.
-
Worn-Out or Stuck Buttons
Physical button degradation develops gradually through normal use as mechanical components experience thousands of activation cycles. Membrane-style keypads particularly suffer from frequent use where pressure-sensitive components gradually lose responsiveness after extended service. Tactile feedback mechanisms within buttons occasionally jam in partially depressed positions, creating operational and feedback issues for users. Environmental contaminants like dust, pollen, or airborne chemical residue sometimes infiltrate button assemblies, interfering with proper contact between elements. Moisture exposure accelerates corrosion on contact points beneath buttons, increasing resistance and eventually preventing proper circuit completion. Our repair specialists utilize specialized cleaning solutions and techniques that restore functionality to contaminated button assemblies without damaging sensitive electronic components housed within the same enclosure.
-
Programming Errors
Code storage and recognition systems occasionally develop corrupted memory that prevents proper authentication despite correct user input. Power interruptions during programming sequences sometimes create incomplete code storage that functions unpredictably thereafter. Multiple reprogramming attempts occasionally overwhelm memory capacity, particularly in older models with limited storage capabilities. Factory reset procedures performed incorrectly might render keypads incapable of accepting new programming instructions despite appearing functional. Temporary memory failures occasionally develop from electromagnetic interference that disrupts stored data without permanently damaging hardware components. Our programming specialists maintain comprehensive knowledge across numerous keypad models, allowing efficient troubleshooting of code-related issues regardless of age or manufacturer specifications that might confuse less experienced technicians attempting repairs.
-
Weather-Related Damage
Outdoor installation exposes keypad units to environmental conditions that accelerate various deterioration processes affecting electronic and mechanical components. Repeated temperature cycles cause expansion and contraction that stresses internal connections and creates microscopic fractures in circuit board solder points. Moisture infiltration through housing seals compromises internal electronics through corrosion processes that worsen until complete failure occurs. Ultraviolet radiation degrades plastic components over time, creating brittleness and increasing vulnerability to impact damage. Freeze-thaw cycles allow moisture penetration followed by expansion that forces internal components apart, breaking delicate connections between electronic elements. Our preventative maintenance recommendations include protective measures like silicone covers and positioning considerations that minimize environmental exposure while maintaining convenient access for daily use.
-
Damaged Wiring
Connection pathways between keypad units and central opener systems represent vulnerable points within the garage access system. Wired keypads depend on intact conductors that maintain consistent electrical connections despite environmental challenges. Rodent damage represents a surprisingly common issue where mice or rats chew through protective insulation, creating short circuits or complete connection failures. Installation errors occasionally leave insufficient wire slack for normal building settlement, eventually creating tension that pulls connections apart. Corrosion gradually develops at terminal points exposed to humidity, increasing resistance until signal transmission becomes unreliable. Weather seal deterioration sometimes allows moisture to travel along wire pathways, causing damage at unexpected points far from prominent entry locations. Our wiring repair procedures include complete pathway inspection rather than focusing solely on obvious damage points that might merely represent symptoms of more extensive problems.
-
Signal Interference
Wireless keypads operate within frequency ranges increasingly crowded by household electronic devices that create competing signals within the same transmission spectrum. New home automation systems, security cameras, and even LED lighting installations sometimes generate electromagnetic interference that disrupts everyday keypad communication. Neighborhood density increases the probability of signal conflicts as adjacent properties utilize similar technologies operating on overlapping frequencies. Construction materials like metal siding or certain insulation types occasionally create unexpected signal blocking or reflection that affects transmission reliability. Power transmission lines near properties generate electromagnetic fields that fluctuate with grid demand, creating intermittent interference patterns that are difficult to diagnose. Our advanced diagnostic equipment includes frequency analyzers identifying specific interference sources, allowing targeted solutions rather than an unnecessary component replacement that fails to address underlying transmission environment issues.
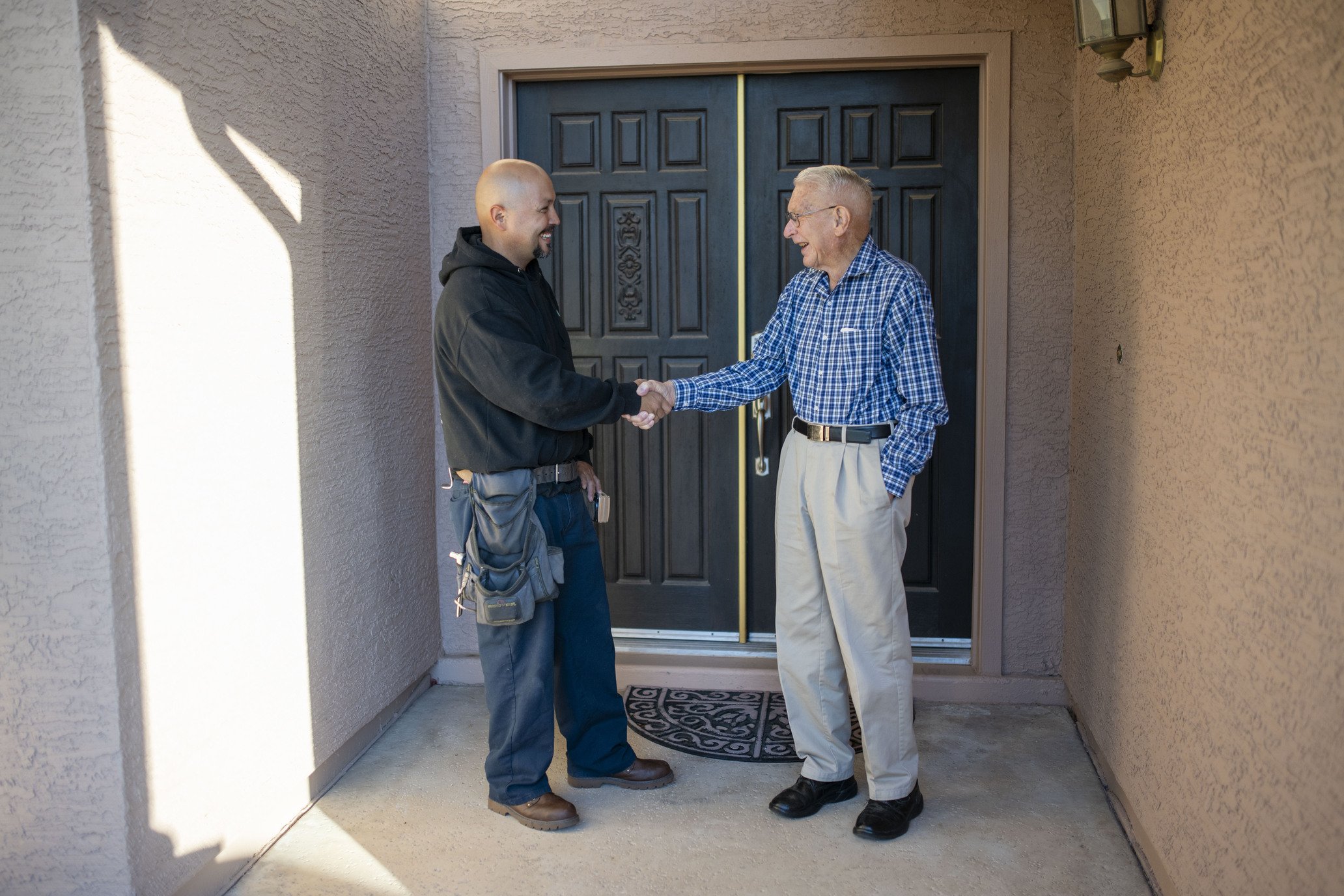
Our Service Areas
Phoenix, Mesa, Chandler, Gilbert, Glendale, Peoria, Scottsdale, Surprise, Tempe, Anthem, Apache Junction, Avondale, Buckeye, El Mirage, Fountain Hills, Goodyear, Gold Canyon, New River, Paradise Valley, Queen Creek, San Tan Valley, Sun City, Sun City West, Sun Lakes, Waddell, and surrounding areas
Our Reviews
Our Garage Door Keypad Repair Process
-
The repair journey begins with a comprehensive examination of the keypad system to identify all contributing factors affecting performance. Our technicians visually inspect the external housing for damage, water infiltration evidence, or mounting issues that might compromise internal components. Battery compartments receive careful attention, checking for corrosion signs that indicate past leakage affecting electrical contacts. Wiring connections undergo a thorough examination, particularly at terminal points where stress or environmental exposure might cause deterioration. Button functionality testing evaluates each key individually, identifying specific problem areas within the input matrix. Communication testing between the keypad and opener unit verifies proper signal transmission using specialized diagnostic equipment that measures signal strength and reception quality. This methodical approach creates a complete understanding of system conditions before proceeding with targeted repair strategies.
-
Once initial diagnosis establishes potential issues, systematic isolation testing begins to confirm specific malfunctions requiring attention. Power supply testing includes voltage measurement across battery terminals or wired connections to verify adequate electrical supply reaching all components. Circuit board examination identifies visible damage like cracked solder joints, burnt components, or corrosion affecting conductive pathways. Communication testing includes frequency analysis for wireless models and checking for interference sources or signal degradation affecting reliable transmission. Programming verification confirms proper code recognition and processing through the entire authentication chain. Environmental testing recreates conditions reported to cause intermittent problems, such as temperature changes or moisture exposure, that might trigger specific malfunctions. This comprehensive approach prevents overlooking contributing factors that might cause recurrence if left unaddressed during the repair process.
-
The appropriate solution depends entirely on specific conditions identified during diagnosis, ranging from simple component replacement to complete keypad upgrading. Battery replacement represents the most straightforward repair, including cleaning contact points to remove corrosion that might affect power delivery. Button mechanisms sometimes benefit from specialized cleaning processes that restore proper tactile response without requiring complete replacement. Circuit board repairs occasionally resolve minor issues like cold solder joints or loose connections when component damage remains limited. Wiring repairs include splice techniques that restore proper connectivity while providing superior environmental protection compared to original installations. Complete replacement becomes necessary when damage extends beyond economical repair, particularly with older models where parts availability presents challenges. Our recommendations always prioritize long-term reliability over temporary fixes that might require additional service visits.
-
Following repairs or replacement, comprehensive verification confirms the complete restoration of proper functionality under various operating conditions. Multiple code entry sequences validate consistent recognition and processing across the entire keypad matrix. Wireless signal testing confirms adequate transmission strength throughout the expected operating range, accounting for potential interference sources in the installation environment. Weather simulation testing for outdoor units includes moisture resistance verification and temperature variation response when these factors contribute to original malfunctions. Battery load testing for wireless models confirms adequate power delivery under peak demand conditions. Communication verification with the central opener unit includes multiple operational cycles to confirm consistent performance. This thorough testing protocol provides confidence that repairs will deliver lasting results rather than temporary symptom masking that leads to recurring issues.
Preventative Maintenance Tips for Garage Door Keypads
-
Replace Batteries Regularly
Proactive power cell replacement prevents unexpected access issues while maintaining optimal system performance. The battery replacement schedule should follow a consistent timeline rather than waiting for obvious performance deterioration that indicates critical power depletion. High-quality alkaline batteries deliver superior performance to bargain alternatives, particularly in wireless keypads exposed to temperature extremes. Battery compartment inspection during replacement allows early detection of corrosion or water infiltration evidence that might require additional attention. Terminal cleaning with appropriate contact treatment solutions prevents resistance buildup that affects power delivery efficiency over time. Battery replacement presents an excellent opportunity for general system inspection that might identify developing issues before they cause complete operational failure. Our maintenance programs include scheduled battery service with comprehensive system evaluation that maintains reliable access while preventing emergencies.
-
Keep the Keypad Clean
Regular cleaning extends operational lifespan while maintaining reliable button functionality that prevents access frustrations. Gentle cleaning solutions formulated explicitly for electronic components remove accumulated grime without risking damage to sensitive internal elements. Compressed air application helps dislodge debris from spaces between buttons that might otherwise interfere with proper depression and contact. Microfiber cloths provide a non-abrasive cleaning capability that preserves protective surface treatments on keypad faces. Special attention to drainage channels and seams prevents water accumulation that might eventually penetrate internal compartments. Cleaning frequency should increase in environments with higher contamination factors like construction dust, pollen, or industrial particulates. Our maintenance technicians utilize specialized tools that access confined areas between buttons without risking damage to delicate mechanical components critical for proper tactile feedback.
-
Inspect for Physical Damage
Regular examination identifies developing issues before they progress to complete system failure requiring extensive repairs. Housing cracks or separation along seam lines creates vulnerability to moisture infiltration, progressively damaging internal electronics. Button membrane deterioration often appears first at edges where environmental exposure accelerates material breakdown. Mounting bracket integrity deserves particular attention, as loosening creates movement that stresses internal wiring connections during keypad use. Drainage port blockage prevents proper water evacuation following precipitation events, potentially trapping moisture against sensitive components. Faceplate discoloration sometimes indicates ultraviolet damage that progressively affects the plastic composition, eventually leading to brittleness and cracking. Our inspection protocols include documentation of developing concerns that might not require immediate attention but warrant monitoring during subsequent maintenance visits.
-
Protect It From Weather
Environmental protection significantly extends the keypad lifespan by minimizing exposure to damaging elements that accelerate component deterioration. Protective covers explicitly designed for keypads shield units from direct precipitation, allowing regular operation without removal. Strategic positioning under eaves or within recessed areas maintains accessibility while reducing direct weather exposure without requiring structural modifications. Silicone sealing along housing seams provides additional moisture barrier protection when factory seals deteriorate. UV-resistant sprays designed for plastic components help prevent sun damage that leads to brittleness and eventual cracking. Water-repellent treatments on external surfaces reduce moisture absorption into micro-pores that might otherwise channel water toward internal components. Our installation recommendations always consider optimal positioning that balances convenience with environmental protection for maximum service life.
-
Check the Wiring and Mounting
Connection pathway integrity remains critical for consistent performance, particularly in wired keypad installations that depend on physical conductors. Mounting bracket tightness verification prevents movement that stresses internal connections when buttons are pressed during everyday use. Wire routing inspection identifies potential damage points where covering deterioration exposes conductors to environmental hazards. Terminal connection examination at both keypad and opener ends identifies corrosion or loosening that increases electrical resistance, affecting signal quality. Strain relief adequacy at housing entry points prevents wire fatigue from repeated flexing, eventually breaking internal conductors. Proper drip loop configuration in wiring prevents water channeling toward electronic components during precipitation events. Our maintenance includes cable path tracing throughout the system rather than focusing solely on visible sections that might appear undamaged while concealing problems elsewhere.
-
Reprogram Access Code Periodically
Security protocol updates maintain access control integrity while confirming proper memory function within keypad systems. Code reprogramming exercises all aspects of the programming sequence, potentially identifying developing issues before they cause complete functionality loss. Memory verification through successful code changes confirms retention capabilities remain intact despite age or environmental exposure. Programming button function testing during code updates identifies specific mechanical issues isolated to this less-frequently used control. Temporary code establishment for service providers or temporary access needs demonstrates programming flexibility while maintaining security through scheduled expiration. Documentation of current codes provides backup information that prevents lockouts requiring emergency service calls. Our maintenance visits include optional reprogramming assistance that maintains security while confirming all programming functions operate properly according to manufacturer specifications.
Choose Lucky Boy Garage Door for Garage Door Keypad Replacement in Mesa, AZ
-
Lucky Boy Garage Door employs specialists with extensive training specifically focused on electronic access systems for residential properties. Our technicians receive manufacturer certification across all major keypad brands, including LiftMaster, Chamberlain, Genie, Linear, and other popular systems installed throughout Mesa neighborhoods. This specialized education includes diagnostic techniques and proper installation procedures that maximize reliability and security. Years of field experience with thousands of successful repairs provide our team with practical knowledge beyond basic training materials or technical documentation. Continuing education requirements keep our specialists current with evolving technology as manufacturers introduce new features and communication protocols. This depth of expertise translates directly into faster problem resolution, more effective repairs, and reliable recommendations regarding repair versus replacement decisions that serve client interests rather than sales goals.
-
Access issues create significant inconvenience and potential security concerns that demand prompt attention from qualified professionals. Our scheduling system prioritizes keypad malfunctions, typically providing same-day service for most Mesa locations when calls arrive before noon. Emergency response capabilities extend to evening and weekend hours without premium pricing that exploits customer urgency. The dispatch system assigns technicians based on proximity and expertise, minimizing travel time while matching specific keypad issues with the most qualified specialist. Service vehicles maintain comprehensive parts inventories for all common keypad models, eliminating delays in waiting for component deliveries in most repair situations. Our efficient diagnostic procedures identify issues quickly without unnecessary disassembly or testing that extends service duration. This responsive approach minimizes property access disruptions while restoring security features promptly, regardless of when problems develop.
-
Our repair philosophy emphasizes client education and transparent options rather than maximizing service revenue through unnecessary replacements. Every service call includes a thorough explanation of identified issues using clear, non-technical language that helps homeowners understand actual conditions rather than technical jargon. Multiple repair approaches receive explanations when options exist, including the advantages and limitations of each potential solution. Replacement recommendations include specific reasoning beyond vague references to age or condition, providing concrete factors that justify investment in new equipment. Cost comparisons between repair and replacement options include long-term considerations rather than focusing solely on immediate expense differences. Our technicians receive compensation based on customer satisfaction rather than sales metrics, eliminating incentives to recommend unnecessary upgrades or replacements that might benefit company revenue at customer expense.
-
Quality keypad service remains accessible to homeowners across various budget ranges through our transparent pricing structure. The detailed estimates provided before work begins include all components, labor, and potential variables that might affect final costs during the repair process. Our volume purchasing arrangements with major manufacturers allow wholesale pricing advantages that translate into consumer savings without compromising quality. Various keypad replacement options accommodate different feature preferences and budget considerations while maintaining essential security and reliability standards. Financing options with favorable terms make immediate installation possible for households preferring monthly payments over single lump-sum investments. Regular promotional offers provide additional value opportunities throughout the year, particularly during seasonal service periods with lower demand volumes. This commitment to value extends beyond initial pricing to include long-term warranty coverage that protects the investment.
Contact Lucky Boy Garage Door LLC
When experiencing garage door keypad failures throughout Mesa, AZ, and surrounding communities, Lucky Boy Garage Door delivers specialized expertise that restores reliable access with minimal disruption. Their certified technicians arrive equipped with comprehensive parts inventories for all major keypad brands, providing same-day solutions for most malfunctions without extended waiting periods. With manufacturer-direct training on the latest wireless technologies and programming protocols, Lucky Boy offers superior diagnostic capabilities that pinpoint exact issues rather than recommending unnecessary replacements. Their reputation for honest assessments, transparent pricing, and warranty-backed installations has made them the preferred choice for homeowners seeking dependable keypad solutions across the East Valley region. The company's responsive scheduling system prioritizes security-related service calls, making them the clear choice for prompt, professional keypad replacement throughout Mesa.